Compared with steel, another important material used in aerospace applications, the advantages of aluminum are obvious.
Although steel is used in applications where strength is critical, aluminum offers important advantages that steel cannot achieve. Aluminum is lighter, has excellent corrosion resistance, and provides the strength required by many aircraft components. Aluminum alloy tube specially designed for the aerospace industry
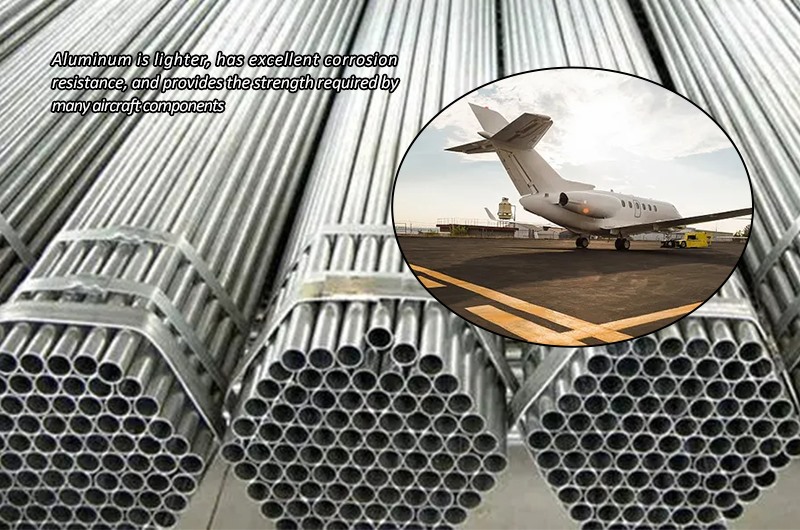
Aluminum Alloy 2014 — This alloy is one of the strongest heat-treatable products currently available. It combines excellent strength and good workability.
Aluminum alloy tube 2014 is one of the easiest aluminum alloys to weld, and it performs well in arc welding and resistance welding methods. However, its corrosion resistance is limited. When exposure to these elements is expected, Alloy 2014 should be covered or painted with pure aluminum for protection. Alloy 2014 is an excellent forged alloy that can be used for aircraft components such as landing gear and hydraulic cylinders.
Aluminum alloy tube 2219 — Another high-strength option, aluminum alloy 2219 relies heavily on applications that require maximum toughness at high temperatures. Alloy 2219 is often used in structural aerospace components-this alloy is used to produce the outer fuel tank of the original space shuttle-because it maintains excellent mechanical properties and workability under annealing conditions. It can also be welded, but it should be heat treated after welding to maintain its corrosion resistance.
Aluminum alloy tube 7475 — has unparalleled strength and crack fatigue resistance, and has the best fracture toughness in the industry. It can also be easily formed and processed under annealing conditions, and the forming can be improved by heating the alloy to 250°F. It is often used for components such as wing spars, wing skins, and fuselage bulkheads.
7178 Aluminum Alloy tube —The main alloying elements are magnesium and copper, making this alloy another reliable choice for high-strength applications. Its toughness makes it a popular material for aircraft skins, especially for protecting components that must withstand compressive stress. When used with oil lubricants, this alloy is easier to process and significantly improves mechanical properties through precipitation hardening. Precipitation heat treatment is carried out at a temperature of 250°F for 24 hours to produce tempering of T6 and T651.