increase the internal surface area of the pipe 2 ~ 3 times, coupled with the turbulent effect formed, the heat transfer efficiency is increased 1. 3 ~ 1. 5 times,
Method for manufacturing inner grooved aluminum tube pipe, including the following steps
I) The aluminum material heated to 460 ~ 510 C is placed in the ingot holder with heat preservation function;
2) The extrusion rod continuously exerts the force on the aluminum material, so that the aluminum material enters the aluminum material channel and the mold, and is extruded from the gap hole of the mold, wherein the extrusion force of the extrusion rod is 600 MPa;
3)During the extrusion process in step 2), the speed measuring device measures the extrusion speed of the extruded aluminum pipe in real time, and controls the extrusion speed of the aluminum pipe to 20 ~ 80m / min. Under the action of the driving motor and the transmission rod, the head rotates correspondingly according to the measured extrusion speed, so that the inner wall of the extruded aluminum pipe forms an internal tooth thread of a corresponding degree.
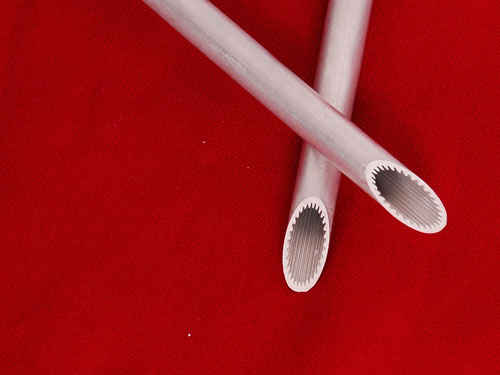
When inner grooved aluminum tube pipe is produced by the method of the present invention, since the internal tooth shape and size are accurately controlled by the internal tooth core head and its corresponding extrusion and rotation speed.Compared with inner-grooved aluminum
tube pipe produced by cold drawing cold rolling process., it has the characteristics of precise and controllable internal tooth shape and size. At the same time, it can also produce and process more aluminum alloy grades, a larger range of product specifications, more complex internal tooth heights and shapes and more precise internal helix angle.