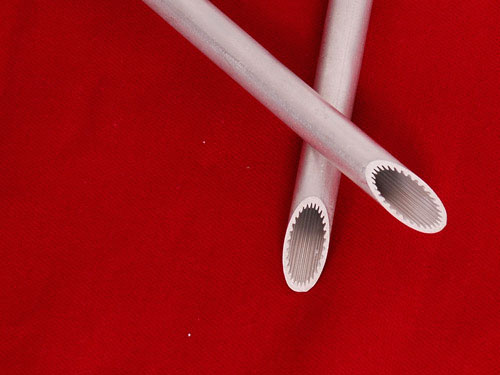
Due to good thermal conductivity, copper and aluminum alloy light pipes have been used as heat exchanger structural materials. With the advancement of material technology, heat exchanger structural materials such as copper internally threaded tubes, heat exchanger aluminum inner groove tube, copper clad aluminum tubes, and copper-aluminum composite threaded tubes have emerged. Ordinary internally threaded tubes are high-end products with grooves on the inner wall and helix angles on the inner wall. The inner wall layer of the inner tube is in contact with the refrigerant to absorb heat, and the outer aluminum tube is used for heat dissipation. Compared with the smooth tube, the common internally threaded tube uses the inner wall groove to increase the heat exchange area and improve the heat exchange efficiency, and the groove with the spiral angle can greatly improve the pressure resistance of the pipe, and has a strong resistance to leakage and resistance Vibration fatigue damage strength makes it safer to use. However, the increase in the internal surface of this common internally threaded tube is limited, and the improved heat exchange efficiency is relatively
In view of the above existing problems and deficiencies, the object of the present invention is to provide a new type of heat exchanger aluminum inner groove tube and its production method, which increases the internal surface area of the internally threaded tube to a greater extent and improves the heat exchange efficiency, while Due to the different heights of the thread teeth of the single spiral thread, it interferes with the circulation of the heat transfer medium and accelerates the heat transfer efficiency.
The invention also provides a method for producing the above heat exchanger inner aluminum groove tube, which successively undergoes steps of corrugated thread forming, annealing, sizing, closing, sub-winding and homogenizing degreasing, wherein corrugated thread forming uses a tube Spinning molding method or metal belt pressure welding method: the tube spinning method uses a spinning machine to spin the inner wall of the pipe. The spinning steel balls in the spinning machine are more than 3, spinning The diameter of the steel ball is 4~30mm, and the spinning speed is 1000~50000r/min.