1 test materials and scheme
1.1 test materials
The test blank is 6060 cast bar with homogenization treatment, and the specification is Φ one hundred and sixty-two × 500mm, see Table 1 for composition. After the cast bar is perforated, it is extruded by 16Mn horizontal hydraulic press. The extruded tube blank is produced after annealing, drawing, quenching and aging. The specification of the sample is Φ eighteen × 2.8mm。 The mechanical property test of the sample is carried out on the wew-300a screen display universal testing machine. The target value of mechanical property of 6060 T6 aluminum seamless pipe is RM, 190 ~ 240mpa and RP0 2≥150MPa、A≥18%。
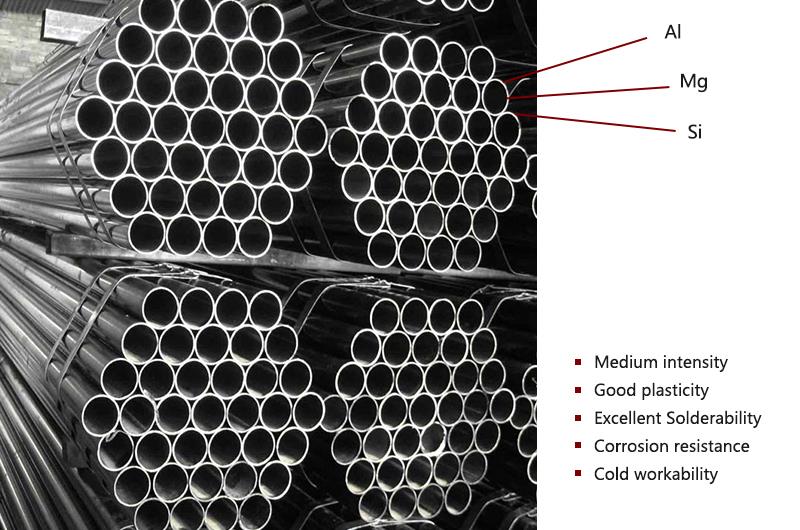
1.2 test process
(1) Test contents: (1) the effect of chemical composition on the mechanical properties of 6060 T6 aluminum seamless pipe was tested with cast bars with three different compositions: A, B and C; (2) Effect of aging process on mechanical properties of 6060 T6 aluminum seamless pipe, including aging temperature and aging holding time.
(2) Test process parameters: (1) melting and casting temperature 700 ~ 750 ℃, casting rod diameter 162mm, casting speed 120 ~ 140 mm / min, casting temperature 685 ~ 715 ℃, water pressure 0.05 ~ 0.10 MPa; (2) Homogenization temperature 570 ℃, heat preservation for 7h; (3) Specification of extruded products 35.2 × 4.6mm, extrusion barrel diameter 170mm, extrusion coefficient 51, casting rod temperature 450 ~ 470 ℃, extrusion barrel temperature 380 ~ 400 ℃, extrusion speed 8 ~ 10 mm / S; (4) Annealing temperature of tube blank (430 ± 3) ℃, holding for 2h; (5) Quenching temperature (530 ± 3) ℃, holding for 2h; (6) Four aging processes, (170 ± 3) ℃ × 2h、 (170±3) ℃ × 4h, (170±3) ℃ × 8h, (200±3) ℃ × 2h。
(3) Production process: solid ingot drilling → extrusion → tube blank annealing → drawing → tube blank intermediate annealing → drawing → quenching → artificial aging → full diameter → finished product sawing.
2 test results and analysis
2.1 influence of chemical composition
The main strengthening phase of 6060 T6 aluminum is Mg2Si, and the ratio of Mg to Si is 1.73 ∶ 1. The impurity phases fe2si al8, Fe Si al5 and Fe Al3 slightly improve the strength of the material. Fe Al3 can refine the grain, and the appropriate addition of Ti can refine the grain and improve the performance index of the material. Under the condition that the Mg content remains basically unchanged, three heats of alloys (a, B and C) with Si content of 0.31%, 0.42% and 0.51% respectively are tested under different aging processes. The test results are shown in Table 2. The tensile strength and yield strength increase with the increase of Si content, while the elongation is the opposite. This result is directly related to the ratio of Mg to Si in Mg2Si, the main strengthening phase in Al Mg Si products. When the Mg content is the same, the higher the Si content is, the excess Si will not affect the solubility of mg2s, which can improve the strength of the material after quenching and aging, but the elongation decreases with the increase of strength, which is consistent with the law of the increase of alloy strength and the decrease of elongation.
2.2 effect of aging process
The sequence of aging desolvation of 6060 T6 aluminum is α Supersaturated solid solution → G.P zone → β〞 Phase → β& apos; Phase → β At the beginning of aging, Mg and Si atoms gather on the crystal surface of aluminum matrix to form solute atom enrichment area, that is, the G.P area maintains a coherent relationship with the matrix, and the atoms on the boundary are shared by the parent phase and G.P area. In order to adapt to the arrangement of two different atoms at the same time, elastic strain occurs near the coherent boundary. It is the serious deformity of this lattice that hinders the movement of dislocations and improves the strength of the alloy. With the increase of aging temperature and time, Mg and Si atoms are further enriched and tend to be ordered, and grow into needle or rod shape rapidly, i.e β〞 The elastic stress field is also the highest when β〞 When the phase grows to a certain size, its stress field is also the highest. From the perspective of desolvation process, G.P area β〞 Phase harmony β& apos; Both phases can effectively improve the strength of the alloy, but their strengthening effects are different β〞 Phase is the largest, once it appears β Phase, alloy strength decreases, so how to improve g. p zone and β〞 The density of phase becomes the key to improve the strength of alloy. G. The number and size of the P-region depend on the aging temperature. The higher the aging temperature, the faster the diffusion of vacancy and solute atoms, and the g.p-region is easy to grow up. Therefore, the size of the g.p-region is larger and the density is reduced. When the aging temperature is above 200 ℃, the G.P zone changes from needle shape to rod shape. Therefore, when aging at 200 ℃, the hardening speed is fast, but the peak time is short, which is due to the combination of G.P zone and β The density of the phase decreases, so its peak value is low. Low temperature aging (170 ℃ aging) is due to its G.P zone and β〞 The phase density is higher than that of high temperature aging at 200 ℃, so its peak value is also higher, but the hardening is slower and the peak time is longer.
According to the above theory, the normal aging process of 6060 T6 aluminum is 170 ℃ × 8h and 200 ℃ × 2H two kinds. 200℃ × The strength value obtained by 2H aging is slightly lower than 170 ℃ × The strength value of 8h aging is because when the effective temperature is 200 ℃, the G.P area changes from needle shape to rod shape, the length increases and the density decreases, so the strength is slightly lower than the strength of 170 ℃ aging temperature, as can be seen from table 2. A. B and C alloys at 170 ℃ × 8h and 200 ℃ × The tensile strength under the two aging processes of 2H is greater than 210mpa, but the elongation is less than 15%, which can not meet the requirement of 18%. By shortening the low temperature aging (170 ℃) time and appropriately reducing the material strength, the elongation of the material can be improved. Table 2 C alloy 170 ℃ × The mechanical property index RM under 4H aging process is 230MPa and Rp0.5 2 is 210mpa and a is 18.5%, meeting the user's requirements.
3 conclusion
(1) 6060 T6 aluminum mg and Si content have a great influence on the strength. When Mg content is constant, with the increase of Si content, excess Si will increase the strength of quenched and aged materials, but the elongation will decrease with the increase of Si content. By comparison, using alloy C, the chemical composition Fe is controlled at 0.14% ~ 0.20% and Si0 51%, Mg0. 50%, Ti content 0.02% ~ 0.04%, and other components are less than 0.02%;
(2) Aging process has a great influence on mechanical properties. Adopt 170 ℃ × 8h and 200 ℃ × 2H aging process, the material strength can meet the standard requirements, but the elongation can not meet the requirements. Shorten the aging time by low temperature aging (170 ℃) × 4h), which can meet the requirements of users.
According to the above process system, the performance target value RM is 190 ~ 240mpa and RP0 2. 6060 seamless aluminum pipe with a ≥ 150MPa and a ≥ 18%.